フォークリフトの安全運転コラム
vol.3|危険を〝未然に発見〟する感受性
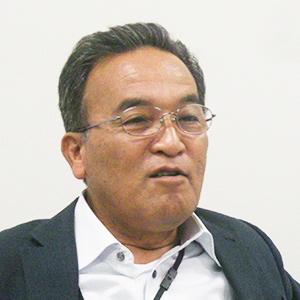
- 文 / 丸山 利明 物流技術研究会
- 大手運送会社に入社後、主に重量物取扱作業に従事する傍ら、社内作業指導員制度設立の一役を担う。
全日本トラックドライバーコンテスト準優勝。全国フォークリフト運転競技大会優勝。
平成15年、現タカラ物流システム(株)入社、平成22年に常務執行役員。
飲料系物流会社と物流技術研究会を設立し現場指導に努力。
陸上貨物運送事業労働災害防止協会(陸災防)専任講師、自動車事故対策機構(NASVA)専任講師などを務める。
現在、(株)TM安全企画を設立し活動中。
![]() |
---|
労働災害はまず予防から
事故から学ぶことは多い。ただ本来事故は未然に防がねばなりません。ひとたびフォークリフト事故が起きれば死亡災害につながりやすく、たとえ人的被害がなくても荷物や商品が傷つき、経済的損失や企業の信頼も失いかねないからです。
事故を未然に防ぐためには、まず危険性をいち早く察知する感受性が何より必要です。今回は職場で実践する危険への感受性向上について考えていきたいと思います。
知識は事故予防に不可欠
危険に対する感受性への第一歩は、知識の会得です。知識と聞くだけで敬遠され、結構おざなりになっている職場が多く残念です。法令や作業の知識、他社や異なる職場の知恵を知ることは、自身の仕事にも役立ちます。
中でも労働安全衛生規則 第151条にはフォークリフトに関する重要な事柄が網羅されています。さらに運転の基本や構造を知っていれば、作業が法令に触れていないか、正しい操作がされているか気付くことができます。
また日常に慣れてしまい危険に鈍感になった時、他社事例などを知っていれば、違った観点で自身の現場を客観的に見直すこともできます。
このように、知識の会得で危険を見極める「目」を持つことができるわけです。知識は働く上で、管理者はもちろん、フォークリフト運転者にも大きな武器になるはずです。
危険な行動と状態を把握
次に大切なのは、現場を見ることです。安全パトロールと呼ばれていますが、歩くだけ見るだけでは意味がありません。
パトロールでは「危険な行動」と「危険な状態」をしっかり把握します。またパトロールする時は管理者単身ではなく、現場をよく知る班長などのリーダーと一緒に巡視します。事前にチェックシートを作り、チェック項目に加え現場から危険を「聞き出す」ことも大切です。積極的に聞き出すためには、知識が必要になってきます。
とある流通加工の製函工程で「仕事中に転落しそうで怖い」と聞き出した事案(図表1)がありました。周囲の者は毎日見ているのに危険視していません。危険に対する感受性は人によって温度差があるものです。だからこそ積極的にコミュニケーションを図り聞き出すことが重要なのです。
図表1感受性あれば危険がわかる
めっきり減った安全の番人
「鬼軍曹」の異名をもつ班長が現場をパトロールして、フォークリフトによる破損事故を激減させた事例もあります。仕事に厳しいリーダーは安全にも厳しいのです。厳しくできるのは感受性が高く知識と熱意がある証拠です。
私が若い頃にも厳しい先輩がいました。フォークリフトに傷が入っていると「こん傷何や!どこで擦ったんや!」と口やかましかった。決まって「荷物見てこい!」となる。その度に荷物の総点検です。
「フォークリフトで飯食うんやったら、フォークリフトに傷つけるな。」と言うのが口癖で、フォークリフトは常に手入れが行き届いていました。当然その部下も皆同じ。後輩たちは少々大変でしたが、この先輩がいたからこそ事故もゼロでした。
今こういう安全の番人は希少価値となりましたが、現場で安全に関するリーダーを育成できれば、事故やヒヤリハットも低減できるのではないかと思っています。
ヒヤリハット活動に工夫を
事故予防ではヒヤリハット活動が有名ですが、いくつか注意も必要です。ヒヤリハットを回収集計する中間管理職にかなり負荷がかかってしまう点です。人手が少ないと、内容を分析しない件数管理に陥りやすい。フィードバック無き集めるだけのヒヤリハットになってしまい、提出する職場も真剣になれなくなってしまう。もうこうなるとヒヤリハット活動は根付きません。
また、他人のヒヤリハットは意外と共感しにくいものです。自分とは違うから自分には起こらないと感じるからです。危険性に共感し感受性を高めるには、フィードバックを動画にしたり、リスクアセスメントで徹底的に撲滅するなど工夫と仕組みが必要です。
リスクアセスメントと現場力
ヒヤリハットが現象ならば、リスクアセスメントはその解決方法です。リスクアセスメントでは、危険性を一個一個潰し、安全が確保されるまで途中で終わることはありません。いわば安全の番人を仕組みに取り入れたものです。また危険度を点数化するため誰にでも一目でわかり、属人的にならないのも利点のひとつです。
ただリスクアセスメントの中には解決に時間を要する対策もあります。しかし事故は待ってはくれません。そんな時に必要なのが現場力です。過去に、電気が暗く危険で天井照明の工事が必要という現場がありました。この職場では知恵を出し合い、自ら補助灯を設置し速やかな環境改善を図りました(図表2)。
これは危険に敏感な職場が自ら行動し解決したものですが、このような職場のボトムアップも事故予防には欠かせないと改めて痛感しました。